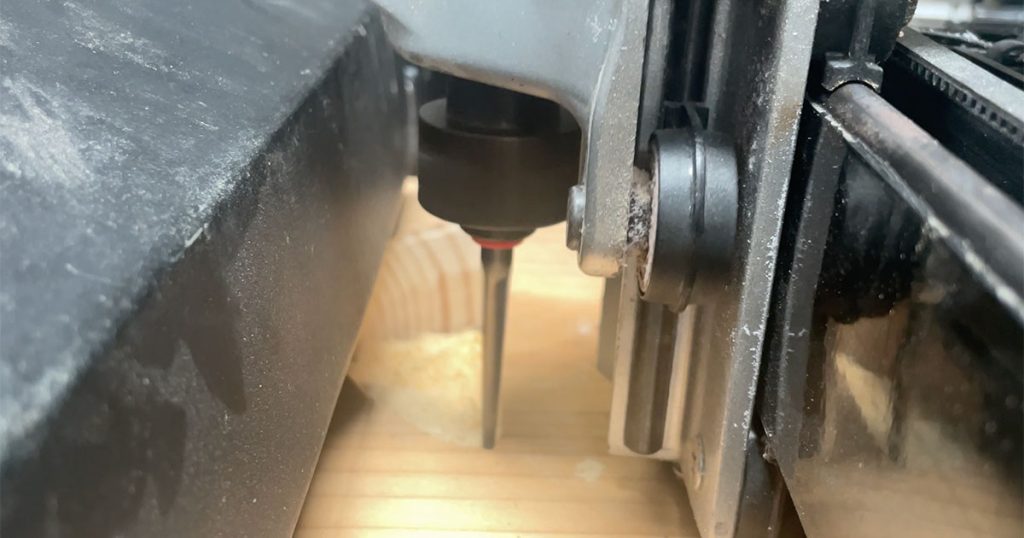
There are many types of CNC router systems on the market today, and they come in many different forms. The most common configuration is the classic flatbed gantry setup, but newer innovations have started introducing other concepts into the market. There is an entire category of portable part-cutting CNC machines now, as well as feed-through CNC systems with large project capacities. Let’s examine and discuss these different CNC router configurations.
Flatbed Gantrys
Flatbed gantry CNC routers are found everywhere in all kinds of sizes, from very heavy equipment requiring a forklift to move to small, DIY kit-based systems that the user builds themselves. All gantry systems are basically the same in form. They have a bed that the material is clamped to, which is attached to rails that command the back and forth (x and y axis) movement of the head. On three-axis systems, the head is also on rails to move up and down (z axis).
The main differences in gantry systems are in their construction. Accuracy in CNC is determined first by the rigidity of the system. To set up a gantry system to be square and its bed parallel requires some effort, so it needs to withstand the load forces of the cutting action at the speeds it is being commanded in order to hold that setup. Industrial machines are very heavily built to handle high speeds and high torque for long periods of time, while the smaller models and kit systems tend to have a flimsier construction resulting in flexing, which requires them to move much slower to reduce the load forces.
PROS | CONS |
---|---|
• Heavy machines tend to be very rigid and hold tolerances well • Good for repeatable part making functions | • DIY and kit systems tend to be flimsy and lose accuracy • Require a large footprint for doing large work • Difficult and time consuming setup |
Portable Part Cutters
There are some CNC routers designed to only cut parts in primarily large-sheet material. Large gantry CNC machines can do this as well, but over the last decade, a few portable variations have been introduced to the market. These range from cable-driven to autonomous wheeled robots and even handheld smart routers that use indexing tape to map their paths. Although some of these machines have had some success, they are incapable of performing 3D carving and are limited to only performing 2D cuts and routing.
As with all CNC systems, accuracy in a portable part cutter is determined by rigidity in its ability to track its movement. Portable systems have a lot of variables to deal with in maintaining accuracy. How tightly is it being held to the board? Are you going too fast for the camera system to keep up? Is there vibration in the board? These are questions one must work around to maintain accuracy.
PROS | CONS |
---|---|
• Portable | • Limited to 2D carves • Difficulties in maintaining accuracy |
Feed-through Systems
CarveWright CNCs, including RAVEN, are the only CNC routers to use a feed-through system. In fact, they own the patent on the concept. Earlier CarveWright models relied on a sophisticated tracking system that used two encoders to track and make position determinations. It required exacting rigidity and board preparation.
The RAVEN CNC has eliminated that complicated system in favor of a tracking belt (AccuTrack) that connects the board directly to a high precision encoder. This allows the CNC to perform precise and repeatable actions every time with little effort. Raven’s rigidity is ensured by its construction. The board is secured to the feed-through drive with the belt system which sets the square precisely. Then it is clamped in place by cranking the heavy cast aluminum head onto the board, ensuring it is perfectly level every time.
PROS | CONS |
---|---|
• Small footprint • Nearly infinite length capacity • Inherently rigid • Easy to square and level | • Limited on width |