RAVEN CNC vs Other CNC Routers
CNC routers have come a long way in a short time. There are a number of options on the marketplace with widely varying capabilities. Choosing the right system can have a big impact on productivity, quality, and overall project success. The cutting-edge RAVEN CNC router system has emerged as a leading contender in this space, offering a distinctive approach to CNC machining that warrants careful comparison with existing solutions.
This analysis examines six critical aspects of CNC systems: user operation, software, size, precision, support, and price. We’ll compare RAVEN CNC’s innovations against traditional competitors’ offerings, and through detailed comparison, we’ll explore how the differences affect both newcomers to CNC machining and experienced users seeking to optimize their workflow.
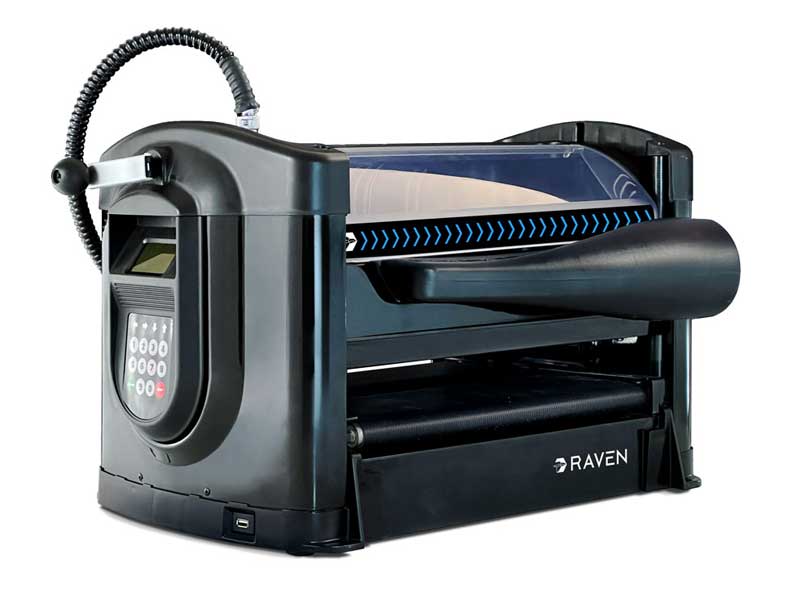
RAVEN CNC Router
RAVEN CNC routers are unique in their use of a feed-through system. In fact, they own the patent on the concept. The board is secured to the feed-through drive with a belt system. Then it is clamped in place by cranking the heavy cast aluminum head onto the board, ensuring it is perfectly level every time and can track precisely. This board feed forms the x axis, while the Y and Z trucks use linear rails to handle the other 2 dimensions for a full 3 axis CNC.
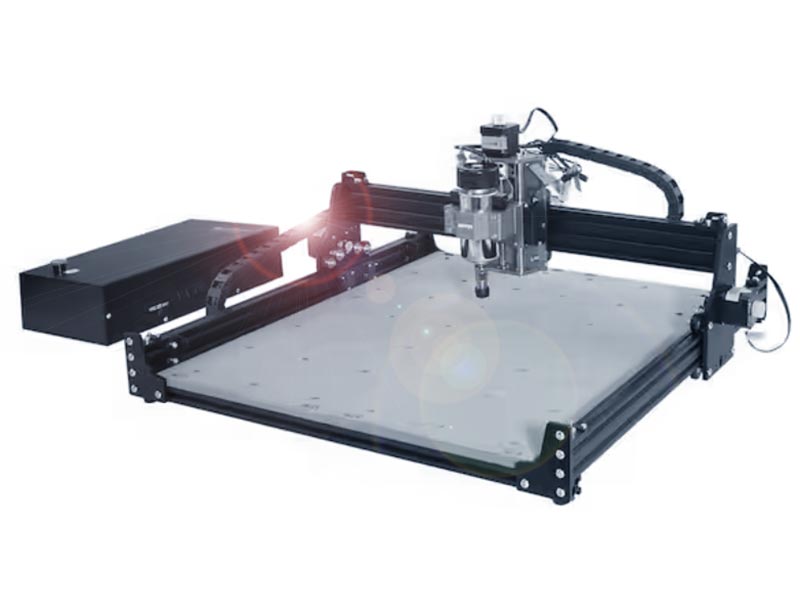
Flatbed Gantry CNC Routers
Flatbed gantry CNC routers are found everywhere in all kinds of sizes, from very heavy equipment requiring a forklift to move to small, DIY kit-based systems that the user builds themselves. All gantry systems are basically the same in form. They have a bed that the material is clamped to, which is attached to rails that command the back and forth (x and y axis) movement of the head. On three-axis systems, the head is also on rails to move up and down (z axis).
User-Friendly Operation
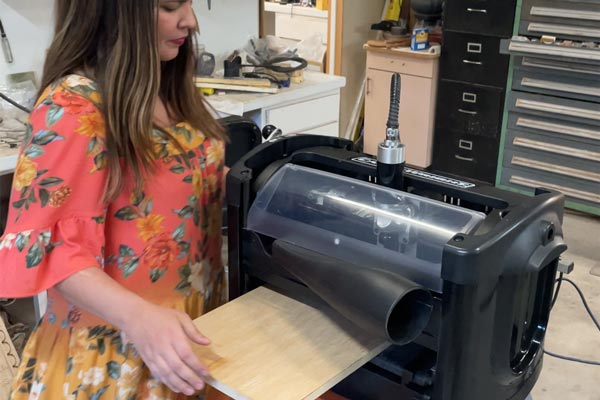
RAVEN CNC Machine
The RAVEN CNC system, including its Designer software, is designed with a focus on user-friendliness. The software offers a clean, intuitive interface, making it accessible to users of varying levels of experience with a full-featured set of tools. The RAVEN’s onboard computer offers a simple, guided setup that gets people carving in minutes. Simply design your project, compile it to a USB drive, and the machine does the rest.
- Simple-to-use, yet full-featured software interface
- Automated post processing by easily compiling to a USB drive
- On On-board computer guides a three-step project setup
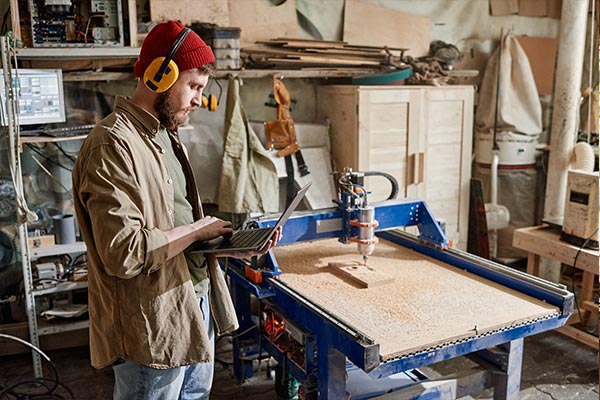
Other CNCs:
Competing CNC systems often come with software that is very simplistic and allows for only the most basic of functions. More capable software can be purchased from third parties, but these can be expensive and difficult to use. Other CNCs use a second piece of software for post processing that requires a computer to be plugged into the machine. Many of these machines are also kits that must be built by the user and require constant leveling and adjusting in order to get your project properly set up a project. These combine to limit the usability for new users and increase the time and effort required to achieve desired results.
- Software lacks features or is expensive and difficult to use
- Require a computer that is connected to the CNC.
- Complicated build and setup procedures
Software
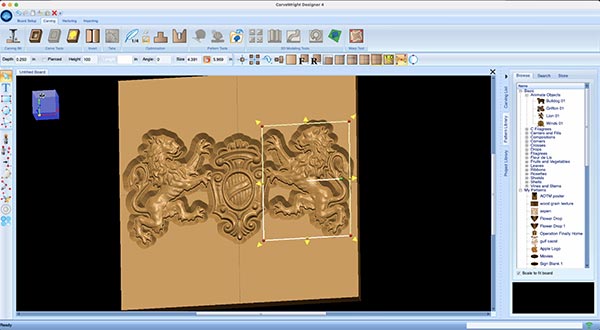
RAVEN CNC Machine
The RAVEN CNC system comes with Designer 5, a fully integrated 3D carving software that is both powerful and user-friendly. It uses a simple drag and drop interface to merge and blend 3D elements to compose original compositions. Draw 2d paths and shapes to define cutouts, routs, and/or pocketing. With add-ons the software can be further built out to suit any needs. Users benefit from a streamlined workflow from design to production that eliminates the need for post-processing software.
- Standard 3D carving capable
- Easy 2D tools for pocketing, routs, and Vcarving
- Drag and Drop intuitiveness
- Automatic tool paths
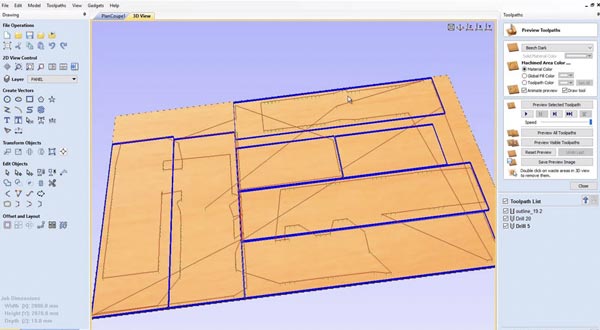
Other CNCs:
The included software with most CNC systems are focused on very basic 2D cutting and pocketing only. To do 3D carving you must purchase expensive and overly complex software. Even then, most of them don’t allow for compositing of more than one 3D model, meaning you can only carve a model as is without the freedom to make your own designs. These software options also require separate post processing software to support and run their machine.
- Most software is only 2D
- 3D-capable software is limited or very expensive
- Difficult to use and learn interface
- Need additional post-processing software
Size
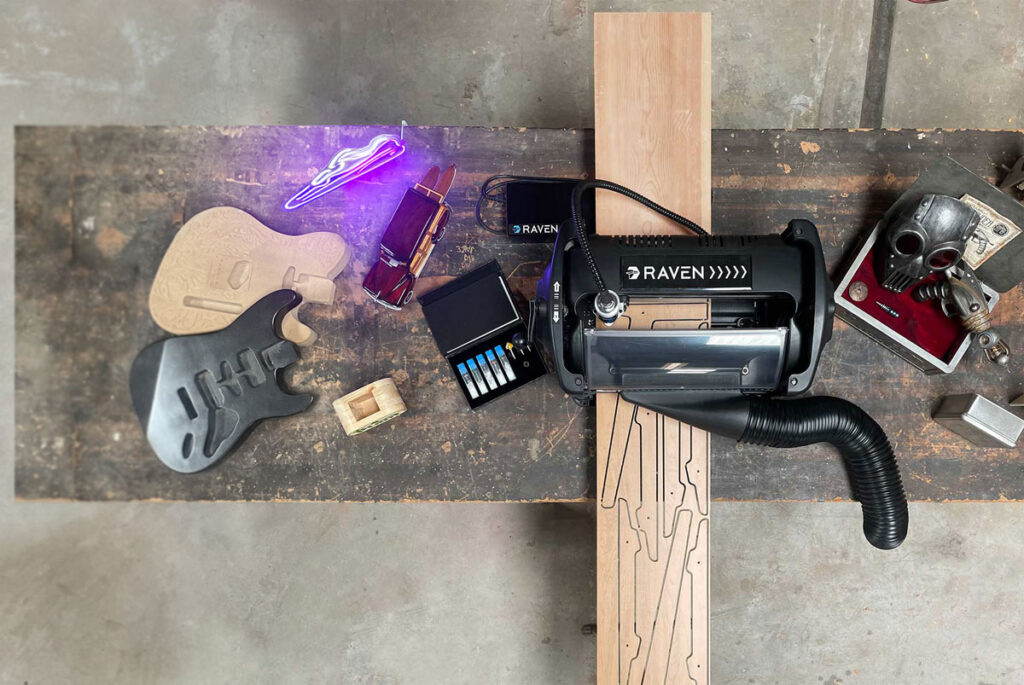
RAVEN CNC Machine
The RAVEN CNC system has the footprint of a portable planer but offers a substantial working capacity of 15.5 inches in width, 5.5 inches in thickness, and up to twelve feet in length. For wide 3D carvings, materials are typically glued together from narrower pieces typically with dowels or biscuits. This technique allows for building at any size and is ideal for materials which are prone to cupping and bowing when carved from one piece.
- Small footprint
- Nearly infinite length capacity
- Easily seam projects together for wider finished pieces
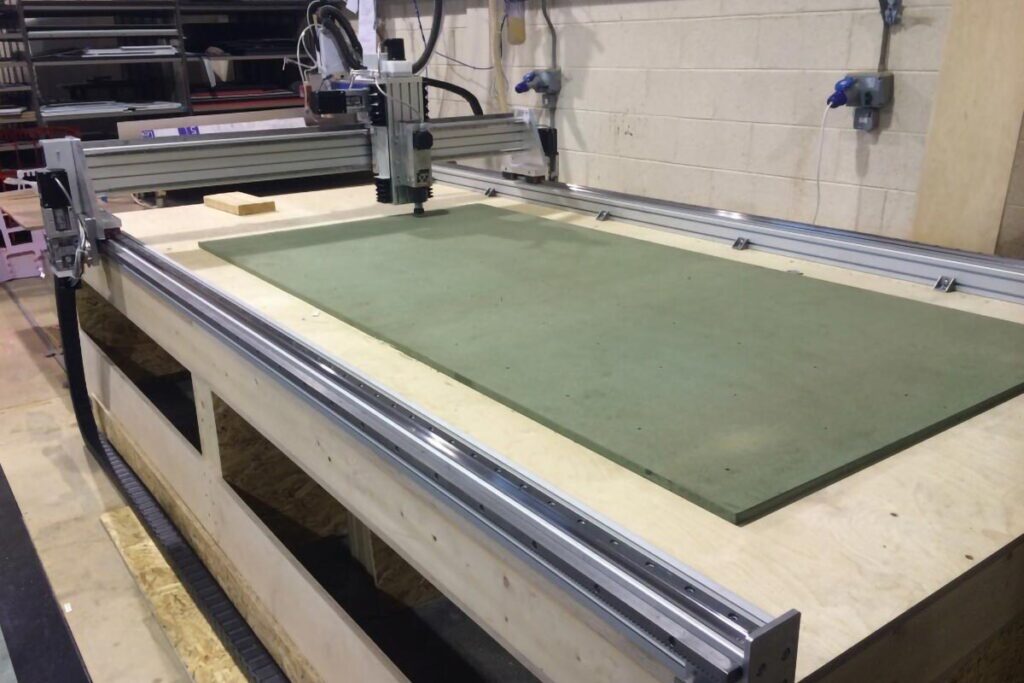
Other CNCs:
Flatbed CNC routers have a bed that material is clamped into. The carving area is determined by the size of the machine making these types of CNC have a much larger footprint relative to their workpiece capacity in all axes. Many options on the market offer more width than a RAVEN, but are limited on length. While seaming 3D carvings across width is possible, it is extremely difficult, if not impossible, to seam across the length.
- Require a large footprint for doing large work.
- Smaller machines limited on length
- Wide boards tend to warp and cup when glued before carving
Precision
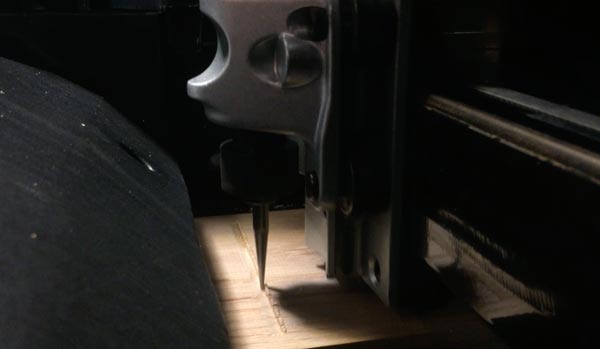
RAVEN CNC Machine
RAVEN CNC machines lead their class in exceptional precision and accuracy, which are crucial for intricate projects. The machine consists of a cast aluminum frame with integrated precision linear rails providing exceptional stiffness and leveling. The machines also use servo axis drives and a brushless spindle motor for a smart sensing system that can auto-react to load conditions in real time. Then the AccuTrack feed-through system ensures 100% accurate feeding of even the roughest material. With these features combined, RAVEN can reliably and repeatedly create at high speeds and load conditions with perfect precision.
- Stiff and rigid design that doesn’t flex or go out of level
- Servo axis drives for real-time sensing of position and load conditions to prevent missteps or crashing
- AccuTrack ensures 100% accurate project feeding
- Able to carve fast
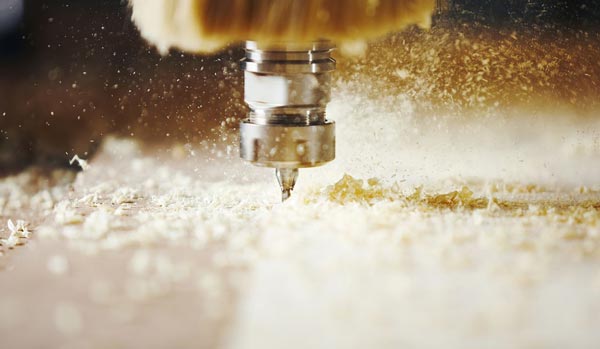
Other CNCs:
While some high-end CNC machines from competitors can match RAVEN’s capabilities, the models in the same price range all use stepper motor drives and relatively flimsy construction. Stepper motors have no sensing, so they have no way of knowing when they have lost position. This results in very slow carve speeds to avoid flexing and misstepping.
- Kit-built machines are relatively flimsy construction
- Stepper motors have no sensing capabilities for reacting to load or missteps
- If speeds are within tolerance levels of the machine, they can be very accurate.
- Machines must carve slowly to avoid flexing and missteps
Support and Maintenance
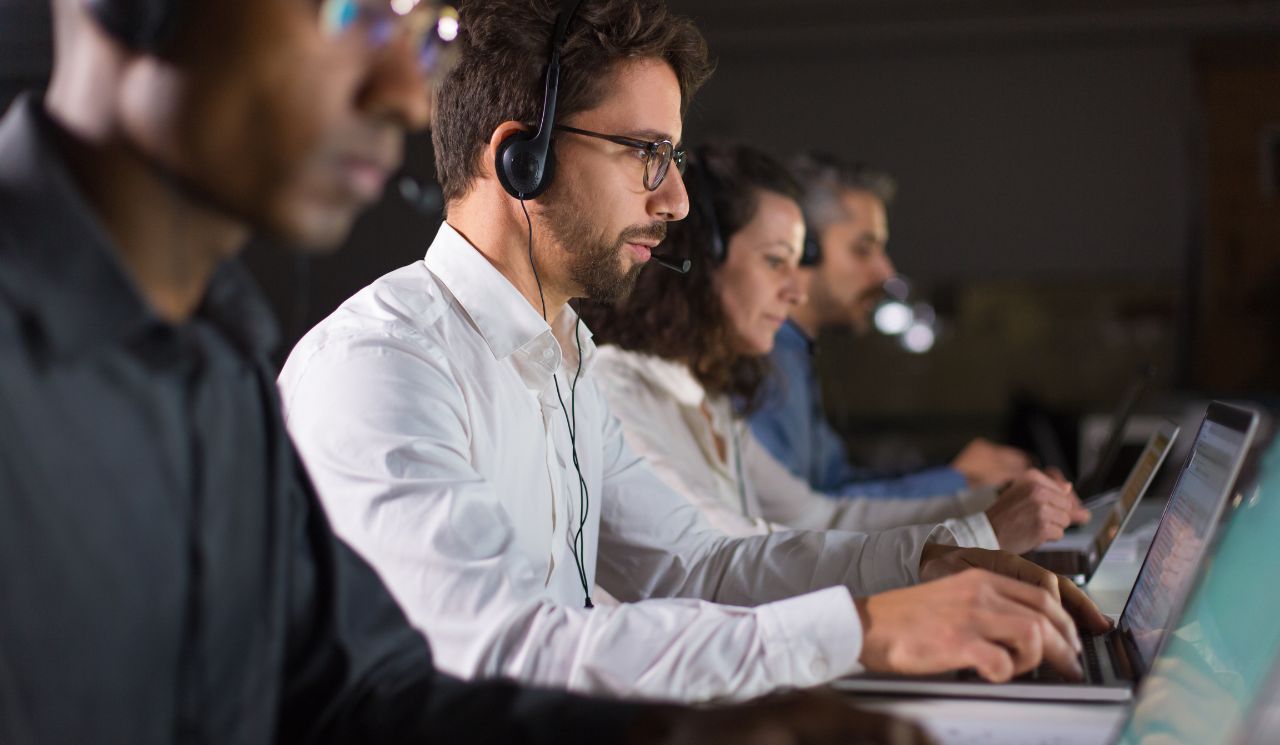
RAVEN CNC Machine
RAVEN CNC offers comprehensive support for its hardware and software, including detailed manuals, online tutorials, and a U.S.-based, responsive customer service team. RAVEN’s onboard computer and servo drives can alert and assist in troubleshooting, limiting downtime. With a brushless spindle motor, there are no brushes to constantly change.
- Comprehensive single-source support for software and hardware
- Onboard computer and servo drives provide alerts and troubleshooting assistance for limited downtimes
- Brushless motor has no brushes to wear
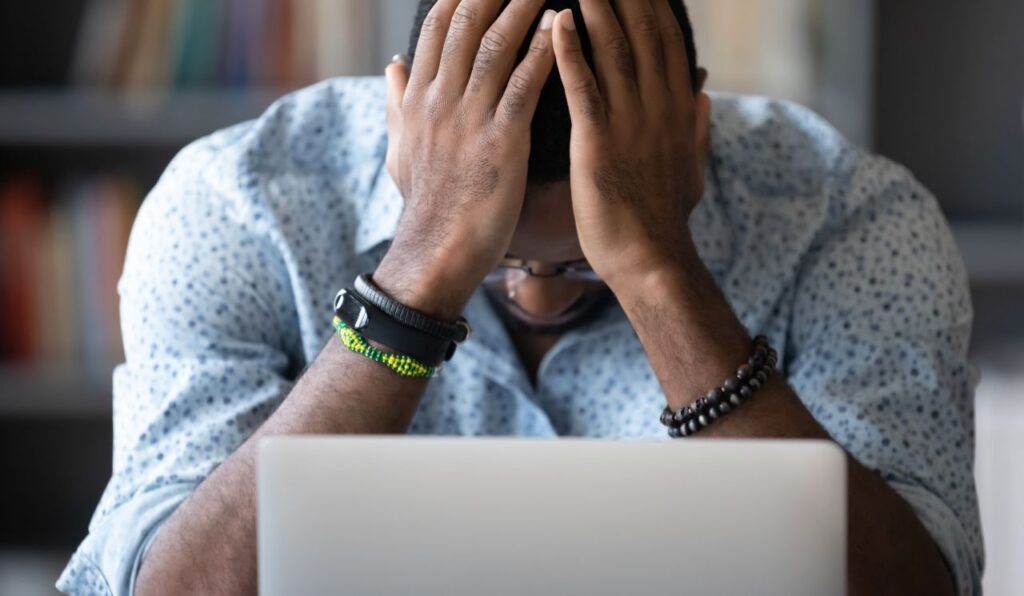
Other CNCs:
Competitors often offer fragmented support, especially if the hardware and software come from different providers. This can lead to longer downtimes and increased difficulty in troubleshooting and resolving issues.
- Disconnected software and hardware support
- No feedback from the machine on the state of its wear
- Off-the-shelf spindle routers wear brushes regularly
Cost Efficiency
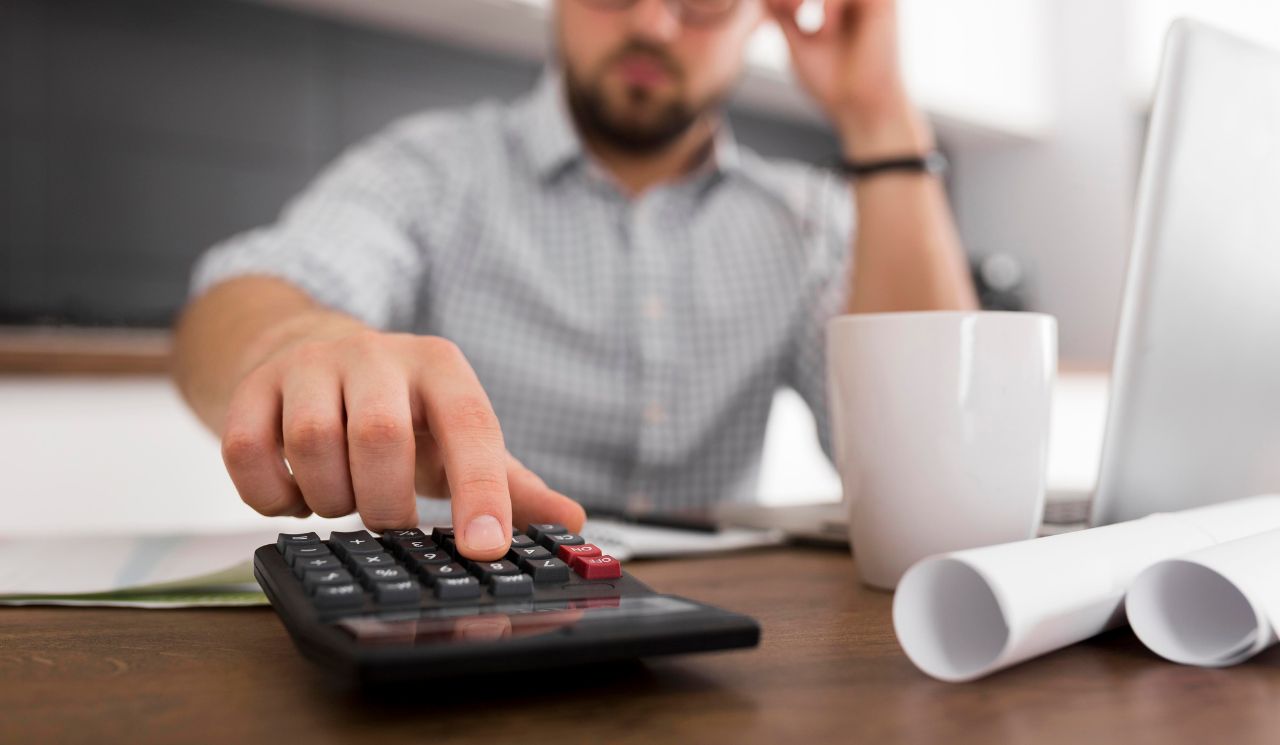
RAVEN CNC Machine
Despite its advanced features and integrated software, the RAVEN CNC system offers excellent value for money. The comprehensive 3D carving software included in the package reduces the need for additional software purchases and minimizes the overall investment. RAVEN also comes with a powerful brushless spindle motor that has no brushes to wear.
- The base machine is a complete system with all needed components
- 3D carving software is included
- Even with everything offered, the cost is less than a comparable CNC setup
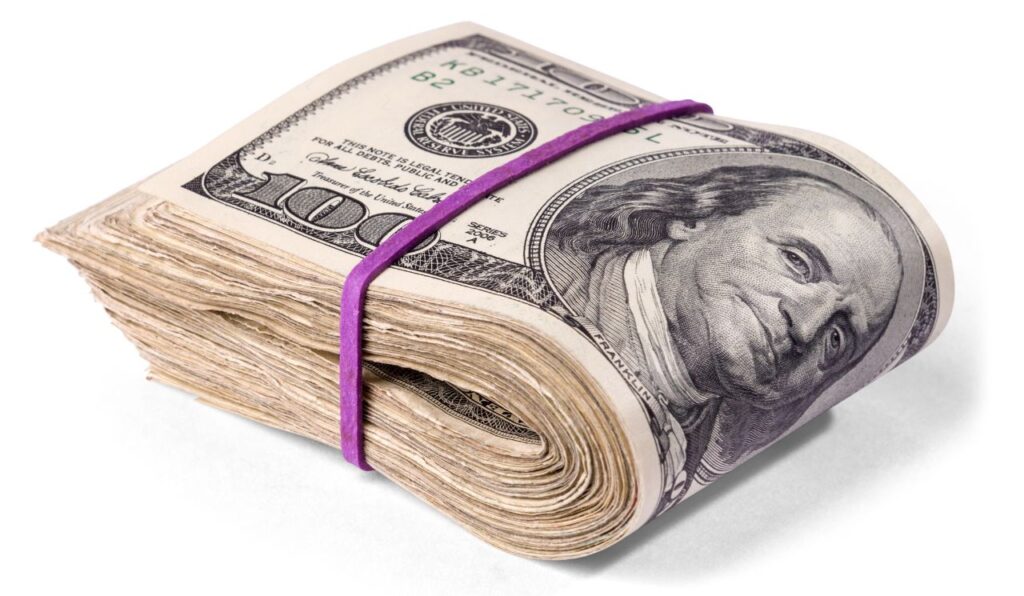
Other CNCs:
Competitors may offer lower initial costs but often require additional purchases for software and accessories to achieve comparable functionality. To start, most machines require an off-the-shelf router to be purchased to strap to the machine. These are brushed motors that aren’t designed for long, continuous use and have a limited lifespan. Spindle motor upgrades can be purchased, but they are expensive. Purchasing software adds significant cost as well. Very quickly, these additional costs can make competing systems considerably more expensive and less cost-effective compared to RAVEN CNC.
- Must choose components which drive cost up
- 3D carving software is an additional cost
- In the end much more expensive
Conclusion
The comparison between RAVEN CNC and competing systems reveals a clear pattern of superior innovation focused on addressing common pain points in CNC machining. RAVEN CNC’s integrated approach combines user-friendly software, efficient space utilization, precise engineering, and comprehensive support to offer a compelling alternative to commonplace CNC router solutions.
While competitors may provide lower initial costs, the total investment in additional software, hardware, and ongoing maintenance can easily exceed RAVEN’s all-inclusive system. By contrast, RAVEN CNC has successfully reimagined the CNC experience, delivering a more accessible, capable, and cost-effective solution for both novice and experienced users. As the CNC market continues to evolve, RAVEN’s comprehensive approach sets a new standard for what users should expect from their CNC systems.